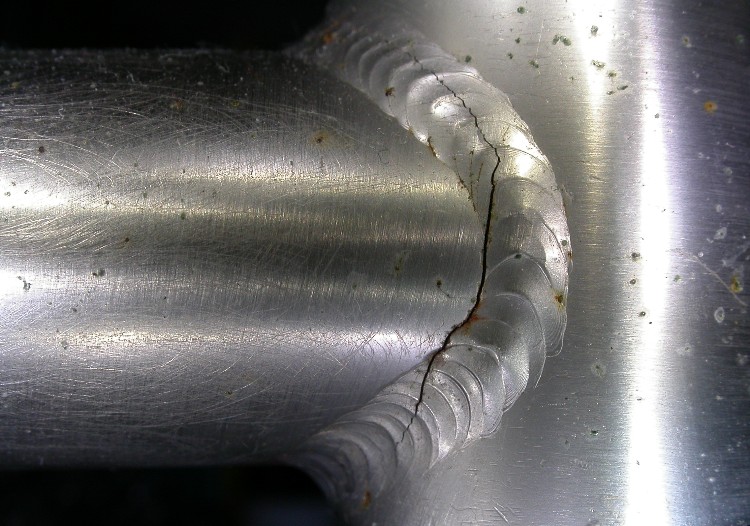
Technical discussion
Welding cracks and preventive measures
advanced options
When carrying out fillet welding operations, partial cracking of the weld bead may occur. How can we prevent and reduce the incidence of cracking in fillet welds?
In recent years, with the development of industries such as machinery, energy, transportation, and petrochemicals, various welding structures have been continuously developed towards functionality and large-scale. Some welding structures also need to work in harsh environments such as high temperature, deep cold, and strong corrosive media. Therefore, the application of various high-strength steels, high-alloy steels, and special alloys has also increased. However, these materials are often prone to various welding cracks.
Usually, welding cracks may occur on the surface of the weld bead and the heat-affected zone, or even inside. Some welding cracks are very fine and not easy to detect with the naked eye. Even methods such as radiographic testing and ultrasonic testing often result in missed detection.
To prevent and reduce the occurrence of welding cracks, it is necessary to first identify their types, characteristics, and causes. This can help welding engineers find appropriate construction and design solutions to prevent cracks. The following will explain in detail the types of welding cracks, preventive measures, and welding design, in accordance with the type of welding crack.